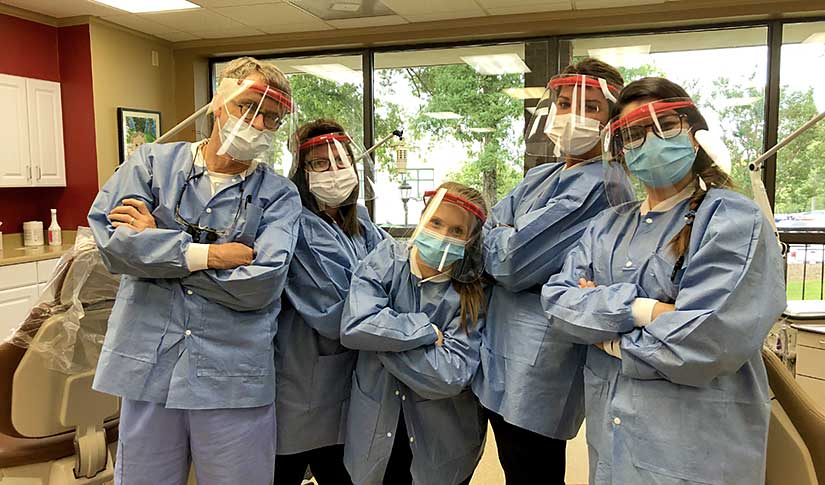
MEMPHIS — Early in the period following Christian Brothers University’s decision to shift to remote learning in response to the threat of the novel coronavirus COVID-19, it became obvious that much of the university’s health science laboratory supplies would be unused and could be put to better use. The CBU School of Sciences and Nursing Program assembled a large stock of gloves, masks, scrubs, and other protective medical gear from the labs and donated them to Regional One Health.
Across campus, in the deserted labs of the Gadomski School of Engineering, there were few such supplies that could be donated. But there was valuable equipment in the mechanical and packaging engineering laboratories that would lay dormant in this new, completely online teaching atmosphere, and professors quickly began to imagine its potential uses in aiding the efforts to protect our healthcare workers in this pandemic.
The professors were not the only ones imagining this possibility. The Tennessee Department of Commerce and Insurance was reaching out to engineering deans and grant officers at colleges and universities across the state offering the possibility of funds to purchase additional necessary equipment to produce much-needed personal protective equipment (PPE) for medical personnel. Bryan Barringer, director of CBU’s Center for Entrepreneurship and Innovation, contacted Dr. Sean June, director of the Gadomski Center for Engineering Innovation at CBU and an assistant professor of Mechanical Engineering, to discuss ideas, the department’s needs, and prospective partners in the private sector.
Dr. June took a quick inventory of the lab equipment — CBU already had 3D printing, thermoforming, and injection molding capabilities, along with a unique Kongsberg digital pattern-cutting table. “There were stories all over about people with 3D printers jumping in and making face masks, face shields, and ventilator parts,” June said. “Face shields were the obvious choice for us to produce.”

Face shields protect medical professionals in clinical settings from heavier droplets and splashes that likely contain pathogens and as a final layer of protection during surgery. They also protect people on the other side of the face shield as well. “They are like the plexiglass shields on salad bars,” June explained, “and those that we are starting to see at grocery stores protecting the cashiers, only much more personal and portable.”
“We didn’t hurry to jump on the 3D printing bandwagon, as we wanted to carefully assess the design, make sure it’s what healthcare providers could actually use, and that it would not do more harm than good,” June added. “We wanted to choose a material that could be printed easily, in large quantities, yet would have the flexibility and strength needed to be useful and safe.”
With rapid partial funding by a grant from the Tennessee Department of Commerce and Insurance Board of Architectural and Engineering Examiners, June purchased additional 3D printers — including small models that could be located in students’ homes or the dorm rooms of students who were still on campus and willing to help out. Luiz Dutra, a senior Mechanical Engineering major, and Chris Fagin, a senior Computer Science/Mathematics major, were quick “dorm refugee” sign-ons. Other student volunteers include senior Mechanical Engineering majors Ian Dover, Christopher Enriquez, and Mario Tellez-Gonzalez, along with juniors Hunter Jordan and Christopher Payne.
“My mother is a Registered Nurse is on the front line fighting this virus daily,” said Payne, who is using two 3D printers in his home. “She uses a disposable face shield and an N-95 mask when she comes in contact with COVID-19 patients. She keeps them in a brown lunch sack in her locker because she is only given one of each per week. When I found out CBU was organizing a project that would combat this issue, I knew I had to get involved. It is exciting to be at a University that supports its community.”
Tellez-Gonzalez is producing headband visors for the shields in his home — “As of right now, we are able to print four visors per day per printer with the 3D printers that Dr. June gave us.” He also gets credit from June for coming up with some g-code — language that the 3D printer recognizes and which tells it how to make the visors — that has improved the process.
Thomas Podesta, a CBU engineering lab technician whom June describes as “lord of the model shop, master of the Kongsberg,” is adding his talents to the process in the on-campus labs.
Coordinating with Barringer and the Center for Entrepreneurship and Innovation, June also partnered with MiBio Medical, a local biomedical data and device company founded by CBU alumnus Ian Rubín de la Borbolla (Mechanical Engineering ’97); Tinker Tech, a local STEM-based education nonprofit founded by University of Memphis student Daniel Smothers; and CBU alumnus Jeremy Hopkins (Mechanical Engineering ’11), a die engineer and “one of the main motivators of this effort,” for additional expertise and assistance. He selected an open-source face shield design offered by Stratasys, a large, well-established pioneer in the 3D printing industry.
The face shields have two parts, a headband and a clear shield. The headbands are 3D-printed and injection-molded. “The 3D printing process that we have chosen for this project works a bit like a hot glue gun,” June explained. “But instead of a solid glue stick, it’s a long piece of plastic forced through a heated tip, which melts the plastic into a thin strand. The thin strands of melted plastic are laid side by side to form a layer of plastic, and the part is built up layer-by-layer until you have a headband. Injection molding is where you have a hollow metal mold, and you inject hot melted plastic into the mold cavity to produce the part. The clear plastic face shields are cut from flat sheets of plastic in large quantities by a computer-controlled knife that can follow the same pattern many times, very quickly.”
Dr. June expects the process to initially manufacture 250 face shields a week, all of which will be donated to Regional One Health. He then expects to ramp up production. “The Gadomski Center has already provided five 3D printers to students and a couple of start-up companies, and my estimates are that we can produce many more than 250 per week,” he predicted. “I also expect that we will have more requests for these printers as word gets out.”
“Great opportunity if you want to borrow a 3D printer for a while and do something good in the process,” he added.
UPDATES
The initial delivery of the first 100 face shields to Regional One Medical Center took place on Thursday, April 16. Since that time, approximately 2,000 face shields have been manufactured and distributed by the CBU team to healthcare professionals in the Memphis area. (As of June 16, 2020)
PHOTOS BELOW:
- A 3D printer in the home of Mario Tellez-Gonzalez, a senior Mechanical Engineering major, and an example of the face shield headbands that it produces.
- The initial delivery of the first 100 face shields took place on Thursday, April 16. Pictured on the left at the Regional One Medical Center loading dock are Charles Blayde (Regional One Health), Dr. Sean June, and Mario Tellez-Gonzalez. On the right are team members Christopher Payne, Chris Fagin, Luiz Paolo Dutra, Mario Tellez-Gonzalez, Daniel Smothers, and Dr. June at CBU prior to making the delivery.
- Dr. Reginald Coopwood (left), president and CEO of Regional One Health, meeting with Dr. Sean June (right) during another delivery of face shields manufactured by the CBU team.
- Dr. William Parris (Class of ’79) and his staff at Parris Orthodontics in Germantown, TN.
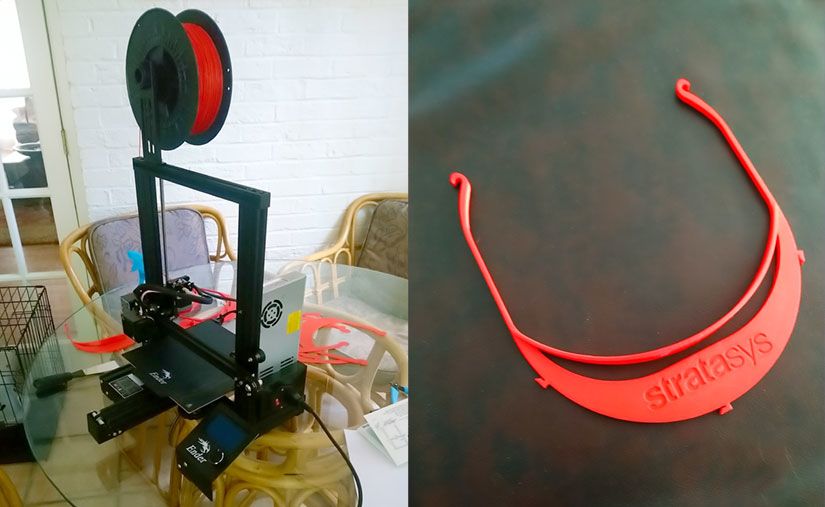
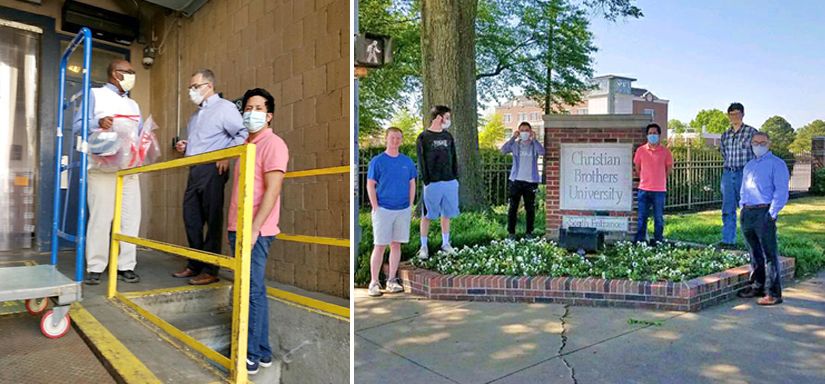
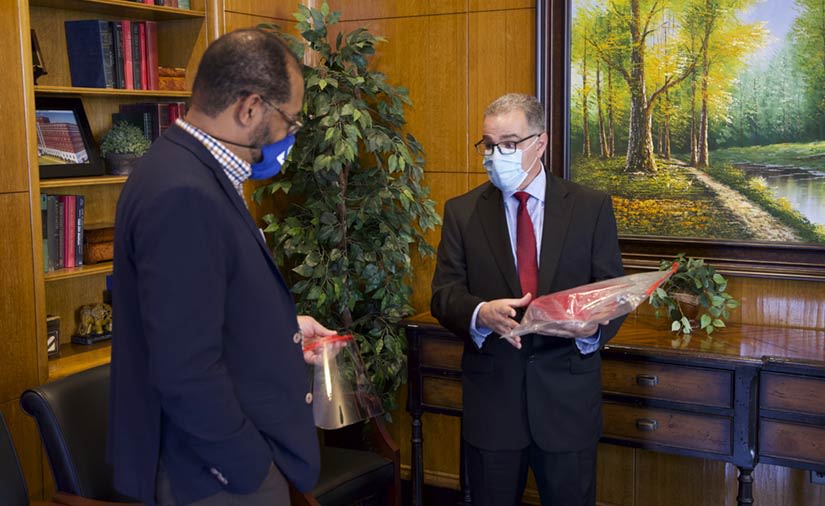
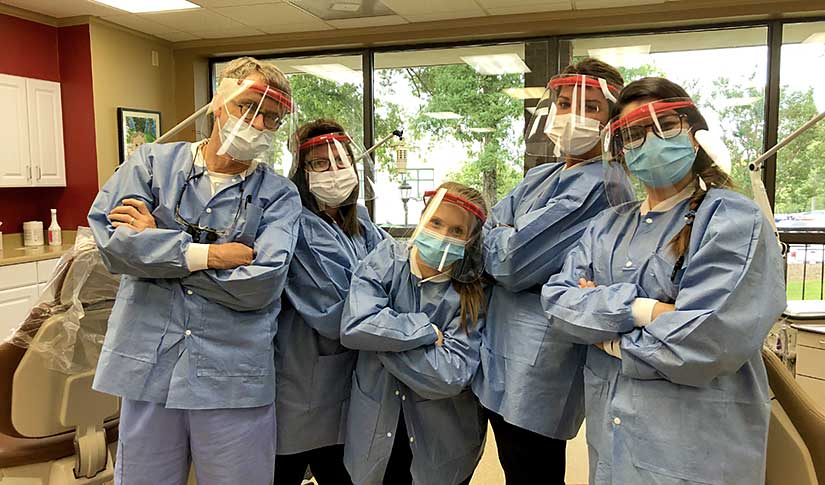